About CMCs
Understanding Ceramic Matrix Composites: ‘’The Essentials’’
According to Composites United report, composite materials consist of a reinforcement, providing strength, and a matrix that binds them. Ceramic matrix composites (CMCs) are a unique subgroup where both components can be ceramic, offering benefits like lightweight, high-temperature stability, and improved fracture toughness. CMCs replace traditional alloys in various applications, including heat exchangers, turbine blades, and braking systems, with growing use in industries like aviation, spaceflight, and electrical engineering. So, the composition of the CMC materials consists of ceramic fibres embedded in a ceramic matrix, producing a reinforced fibre-reinforced material. There are two basic composite categories: oxide CMCs and non-oxide CMCs.
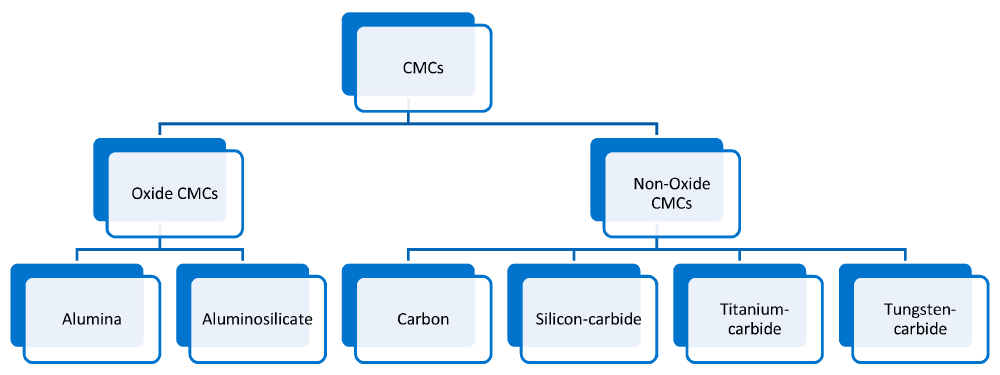
The CMC market is characterized by various factors such as their composition of materials from which they are made, or their manufacturing process. These factors determine its technical characteristics, its costs and therefore its feasibility and viability to be applied by end-users.
Processing of CMCs
The processing of CMCs is structured in three steps:
First, the lay-up and fixation of the fibres, formed according to the required component geometry.
Then, the infiltration of the matrix material, which requires different procedures with differences according to the base material.
Finally, machining and sometimes coating or impregnation of the intrinsic porosity.
The main fabrication processes used for CMCs include Chemical Vapor Infiltration (CVI), Polymer Infiltration and Pyrolysis (PIP), Reactive Melt Infiltration (LSI), and hot press sintering techniques. Polymer infiltration and pyrolysis are the most commonly used ones. Every process has different positive and negative attributes.
A major criterion to select the most appropriate manufacturing system is the price per unit volume of the ceramic matrix and fibre used, as well as the environmental impact of the material (considering the extraction, processing, and delivery of the constituting materials to the CMC fabrication plant). This environmental impact can be quantified through the use of embodied energy, which accounts for the energy consumed by all manufacturing processes used.
According to this quantification, “aluminosilicate CMCs have the highest embodied energy as they have some of the more complex material compositions. This indicates that the manufacturing process used to compose this type of CMCs (sol-gel infiltration, sintering) requires a lot of energy and time, increasing the final cost of the production of aluminosilicate-based applications. On the other hand, carbon matrix, alumina oxide, and silicon carbide CMCs have lower embodied energy, meaning that these materials are easier to produce at larger production rates with lower overall costs and faster time scales. This is because their process materials have fewer complex compositions as they include smaller amounts of fibres and matrix materials”.
Fibers for CMCs
a) Fibers for non-oxide CMCs
Silicon carbide (SiC) fibers, ranging from 5 to 150 micrometers, offer high stiffness, tensile strength, chemical resistance, and temperature tolerance, making them ideal for aerospace applications like gas turbines. The most common manufacturing process, the Yajima method, converts preceramic liquid polymers into SiC fibers, widely used by companies like Nippon Carbon and Ube Industries. An alternative method, chemical vapor deposition (CVD), grows SiC on a carbon core, while laser-driven CVD (LCVD) allows rapid fiber growth. SiC fibers are predominantly used as reinforcement materials in ceramic matrix composites for high-temperature applications.
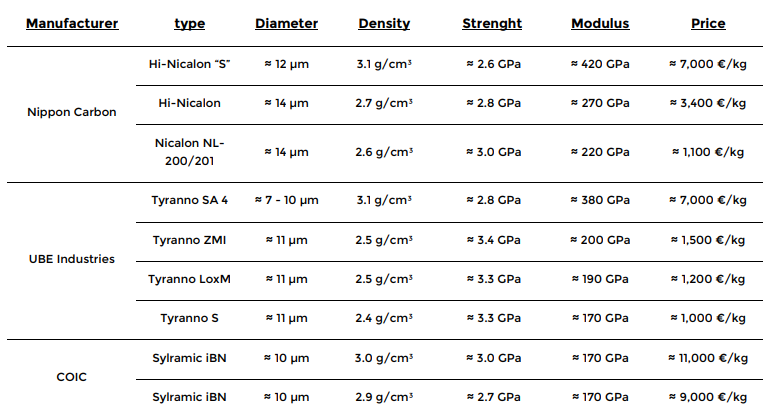
Other suppliers, like Speciality Materials and Tisics, produce SiC fibers with a core, while BJS Ceramics is collaborating on launching a European SiC fiber. General Electric has developed its own in-house SiC fiber production, surpassing global capacities of other manufacturers.
b) Fibers for oxide CMCs
The only oxidic ceramic fibers available are mainly based on aluminum oxide, sometimes mixed with silicon dioxide, boron oxide, or zirconium oxide. Mullite fibers, composed of 85% Al₂O₃ and 15% SiO₂, are polycrystalline. Spinning masses with organic polymers ensure fiber formation, which is then sintered to create finished oxidic ceramic fibers.
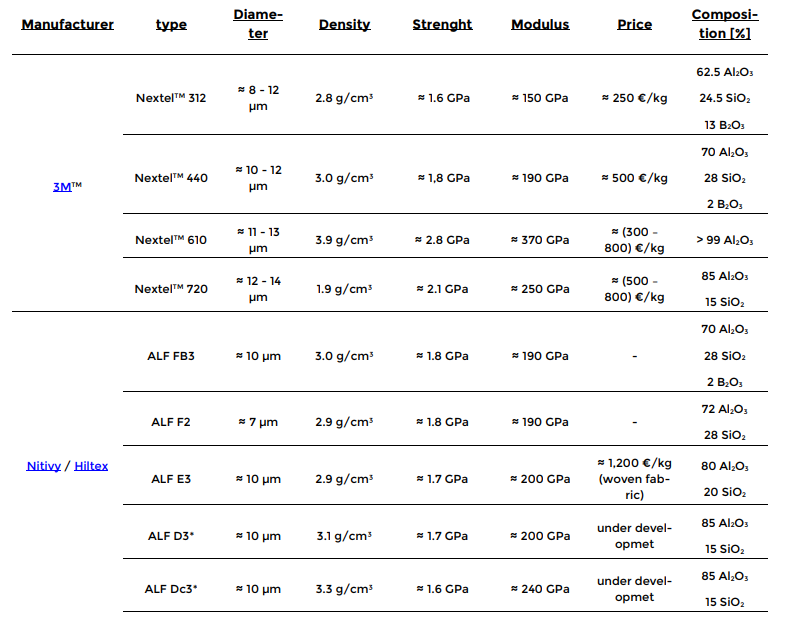
Nextel™ 610 and 720 dominate the high-performance oxide CMC market, with other suppliers like Nitivy, Rath, and Saint Gobain developing new fibers. Nitivy is working on Al₂O₃ fibers, while Rath and Saint Gobain aim to introduce competitive fibers by the mid-2020s.